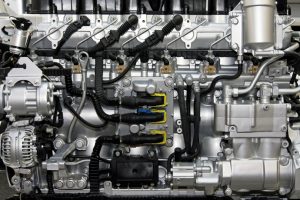
Modern diesel engines require cleaner diesel fuel to meet the needs of the injection system pumps and injectors. Keeping diesel clean has become more complex due to higher concentrations of water emulsions in the fuel and organic contaminants that can pollute the system.
Advances in diesel filtration are helping to meet the growing cleanliness requirements of modern engines to boost performance. Here are five brief points about diesel quality and technology:
High-pressure common-rail fuel systems, known by the acronym HPCR used in low-emission diesel engines are much more sensitive to damage from contaminants 20 times smaller than the diameter of human hair. For engine manufacturers, this means stricter requirements for fuel filtration.
Today the industry is measuring high efficiency closer to 99.9 percent for particles in the 4-micron range.
A fraction of a percent can make all the difference in achieving fuel cleanliness requirements for HPCR components.
Water in the diesel supply is a significant obstacle to achieving the best performance and can also cause fuel filter clogging, injector buildup, diesel fuel instability, and even bacterial growth in onboard and storage tanks. As a result, primary filters are transitioning to an advanced filtration technology called coalescing filtration, which features multi-layered filter media and multiple filtration and separation steps to collect the finest micro water droplets into larger droplets to be able to more easily remove from fuel.
Modern ultra-low sulfur fuels have generated the need for additives to replace the lubricating properties of sulfur-based compounds. Surfactant-based fuel additives with good fuel solubility characteristics are useful because they bind to a wide range of surfaces and help maintain fuel purity. But they must be used correctly.
Although glycerin and related byproducts of biodiesel production are found in synthetic fuel blends of plant origin, they will not cause immediate problems as long as they remain hot and in liquid form.
The exact percentage of the mixture, the temperature, and the water content can influence the amount of glycerin a fuel can contain in the solution. When glycerin precipitates or separates from the solution, it can adversely affect filterability similar to excess additives and dramatically reduce the expected filter life. To help mitigate this problem, it is important to look for blends with lower glycerin levels.
Modern high-efficiency filters intercept the finest contaminants, which could in the past pass without problems nowadays be a contributing factor to clog a finer filter.
Fuel cleaning is the first line of defense against downtime and high operating costs. Contaminants in diesel such as solid particles, dirt, water, and organic particles can have deleterious effects on injection system components, some of which can pose serious warranty and total cost of ownership issues.
In addition to the final filtration of the diesel, it has become particularly important to keep the diesel fuel clean in the onboard and storage tanks as biofuels present a further problem linked to the proliferation of mucilage and algae that find a fertile environment with the presence of water.
To provide an overview of the problems, requirements, and regulations, we have prepared a document that deals with the topic of cleaning, the relative regulations, and the possibilities we can offer to remedy these problems, guaranteeing a fuel of a quality that is appropriate and adequate to the needs. of modern engines and their injection systems.
Here the download Link